Порошковая Металлургия, No. 5(281), с. 40-44, 1986
УДК 666.76.01+621.48
Ю.Гогоци, А.Гогоци, О.Щербина
ВЛИЯНИЕ ОКИСЛЕНИЯ НА ПРОЧНОСТЬ РЕАКЦИОННОСПЕЧЕННОИ КЕРАМИКИ НА ОСНОВЕ НИТРИДА КРЕМНИЯ
Порошковые материалы, изделия и покрытия
Керамика на основе нитрида кремния перспективна для изготовления деталей различных высокотемпературных устройств [1]. Ннтридокремниевые материалы могут сохранять высокую прочность до температуры 1200—1400 °С. Причем, как было показано ранее [2], их прочность определяется состоянием вторичной межзеренной фазы: чем выше температура ее размягчения, тем больше допустимая для данного материала рабочая температура. Температура размягчения межзеренной фазы зависит в основном от вида введенной в материал добавки (MgO или другой) и содержания примесей (Са, Fe, AI).
Очистка исходного сырья от примесей увеличивает высокотемпературную прочность реакционно связанного Si3N4 на 15% [3]. Отрицательное влияние примесей в данном случае связано с тем, что они понижают температуру ликвидуса межзеренной фазы и препятствуют ее кристаллизации. При окислении в процессе эксплуатации в результате диффузии кислорода по порам и границам зерен в глубь материала в приповерхностных слоях образуется жидкая силикатная фаза с температурой плавления около 1100 "С [4]. В то же время минимальная температура плавления чистой системы MgO—S1O2 составляет 1540°С. В процессе окисления наряду с проникновением кислорода вглубь происходит диффузия примесей к поверхности.
Таким образом, при окислении нитридокремниевых материалов примеси перераспределяются по объему и концентрируются в тонкой поверхностной пленке. Авторы [6] считают, что таким путем можно очистить основную массу материала от примесей и добиться повышения его прочности при высоких температурах. При этом рекомендуется удалять насыщенный примесями и содержащий много дефектов поверхностный оксидный слой. Окисление горячепрессованного нитрида кремния в течение 300 ч при 1400 °С повышает прочность при этой температуре более чем на 50 % [6[. При этом критический коэффициент интенсивности напряжений К\с уже после 5 ч окисления, а затем удаления оксидного слоя повышается на 50 % [6].
В связи с тем что детали сложной формы изготавливают в основном методом реакционного спекания, а не горячим прессованием, большой практический интерес представляет применение описанного способа повышения прочности и трещиностойкости к реакционно спеченным материалам. Известно, однако, что свойства горячепрессованных и реакционноспеченных материалов сильно отличаются [4], поэтому окисление может оказывать на них различное влияние.
В настоящей работе исследовано влияние окисления с последующим удалением оксидного слоя на прочность реакционно спеченного материала типа НКККМ-83 системы Si3N4—SiC (70:30), содержащего 2 % MgO в качестве активирующей спекание добавки, при температурах 20 и 1400 °С. Исходным сырьем служил порошок кремния марки КПС-3, в котором при помощи спектрального анализа были обнаружены примеси Ti, Си, Al, Ni, Мп в количествах от 0,1 до 0,01 %. Йа-мол железа составлял около 0,6 %. Механизм и кинетика окисления материалов типа НКККМ описаны в работе [5], их механические свойства — в работе [7].
Образцы для испытаний вырезали из заготовок размером 5.5Х5.5Х Х55 мм. Часть из них подвергали предварительному окислению при 1400°С в течение 5 ч (таблица). При выборе времени окисления руководствовались следующими соображениями. Реакционно спеченные материалы обладают меньшей стойкостью к окислению, чем горячепрессованные. Выдержка материалов в окислительной среде более 5 ч не приводит к дальнейшему изменению их прочности [8]. На поверхности таких
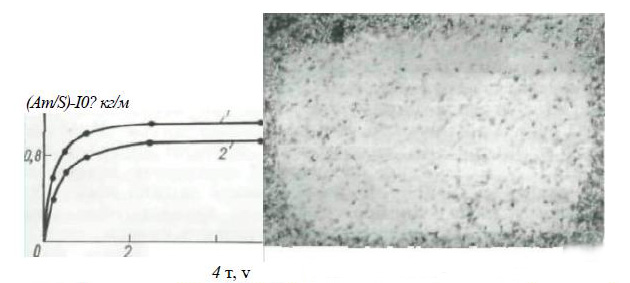
Рис. 1. Зависимости приращения массы на единицу плошали геометрической поверхности образцов групп I (/) н 2 (2) от времени окисления.
Рис. 2. Шлиф среза образца группы 3. Х16.
образцов[5] при 1400 °С защитный слой формируется в первый час окисления, и скорость процесса после этого резко замедляется. Уже после 5 ч выдержки горячепрессоваиного Si3N4 при 1400 °С величина К\с увеличивается в полтора раза.
Испытания проводили методом трехточечного изгиба на установке МИК-9 [8]. Предел прочности рассчитывали без учета нелинейности диаграмм деформирования по известной формуле сопротивления материалов: 0у.н= (ЗР • а) / (Ь • li2), где Р — разрушающая нагрузка; а — длина консольной части образца (10 мм). Ширина Ь, высота h образцов, подвергнутых различным видам обработки, немного отличались, однако
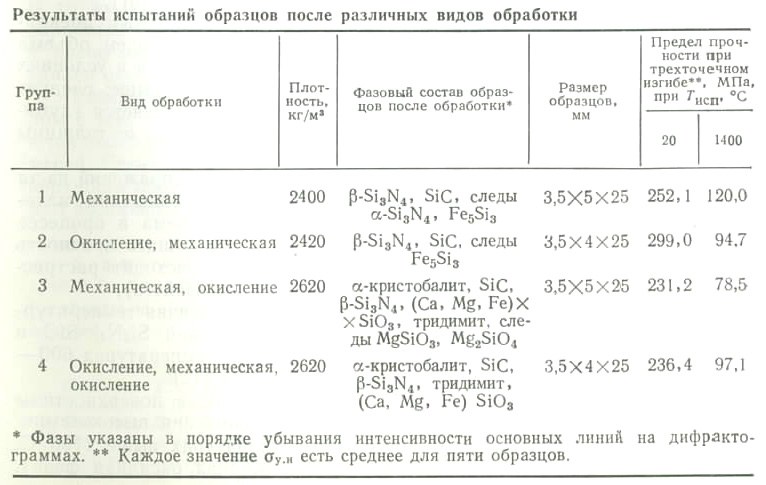
настолько, что, как было показано в [9], влиянием масштабного фактора можно пренебречь. Рентгенофазовый анализ материала проводили при помощи дифрактометра ДРОН-2,0 в Си/(а-излучение). Шлифы и изломы образцов исследовали на металлографическом микроскопе «Неофот-21».
После 1 ч нагрева процесс окисления стабилизируется и его скорость замедляется (рис. 1). В результате окисления по указанному режиму на поверхности образцов образуется блестящая оксидная пленка толщиной примерно 10 мкм. При этом также значительно видоизменяется состав и структура материала на глубину до 1 мм (рис. 2). В связи с этим механическую обработку окисленных заготовок проводили с таким расчетом, чтобы наиболее полно удалить поверхностный слой и исключить его влияние на результаты испытаний. Рентгенофазовым анализом в составе обработанных образцов не обнаружено никаких кристаллических оксидных фаз. В состав поверхностного окисленного слоя входили диоксид кремния в виде а-кристобалита и стеклофазы, силикаты сложного состава типа диопсида (Са, MgJSiCu и аугита (Са, Mg, Fe)SiCb, силикаты магния — энстатит MgSi03 и форстерит MgSi04. Содержание кристаллических соединений магния, железа н кальция (5—10 % по массе) превышало нижний предел чувствительности дифрактометра. Следовательно, примеси, обладающие высоким сродством к кислороду, концентрируются в топкой пленке на поверхности образца. Добиться кристаллизации примесных фаз в оксидном слое удалось медленным охлаждением образцов вместе с печью. При быстром охлаждении они входят в состав стекло-фазы [5|.
С увеличением температуры испытаний от 20 до 1400 °С предел прочности образцов уменьшается более чем вдвое (таблица). Причем наибольшую прочность при 1400 °С имеют образцы, не подвергавшиеся предварительному окислению. Об отрицательном влиянии окисления при 1400 °С на прочность реакционноспеченных нитридокромниевых материалов сообщалось и ранее [8]. На основании полученных нами ранее результатов [5, 8, 10] и данных работ [6, 11] можно сформулировать причины изменения прочности материалов после окисления:
Залечивание пор, трещин и других дефектов в поверхностных и во внутренних слоях образцов (это, по-видимому, основная причина повышения прочности образцов после окисления; примерно такого же ее увеличения можно достичь путем шлифовки поверхности [81);
растрескивание поверхностного слоя, вызванное фазовым превращением в кристобалите, которое сопровождается изменением объема па 5 % [12] (это часто обусловливает понижение прочности в условиях комнатной температуры после окисления при 1100°С и выше; следует также учитывать, что уровень падения прочности определяется глубиной возникающих трещин, которая, в свою очередь, зависит от толщины оксидной пленки);
возникновение в поверхностном слое сжимающих напряжений из-за разницы температурных коэффициентов линейного расширения материала и оксидного слоя и вследствие увеличения объема в процессе превращения Si3N4 и SiC в SiOo (все это может повышать прочность [8], однако при слишком больших напряжениях происходит растрескивание оксидного слоя и деградация прочностных свойств);
возникновение напряжений при нагреве из-за различия температурных коэффициентов линейного расширения соединений Si3N4, SiC и межзеренной вторичной фазы, наблюдающееся при температурах 600— 900 °С и несколько снижающее прочность материала [11];
травление границ зерен и образование по ним в поверхностном слое жидкой фазы [13] (это одна из причин понижения высокотемпературной прочности после окисления при температурах выше 1100°С, когда па поверхности материала образуется жидкая оксидная фаза).
Более низкая прочность при 1400°С предварительно окисленных образцов, по-видимому, вызвана влиянием последнего из перечисленных факторов. Отметим, что образцы групп 2 и 4 (таблица) имели на 15—20 % более высокую прочность, чем образцы группы 3. Это связано с тем, что благодаря предварительному окислению и удалению оксидного слоя они содержали меньше примесей и образующейся при их окислении жидкой фазы, которая к тому же имела большую вязкость. Уменьшение содержания примесей в этих образцах подтверждается данными рентгенофазового анализа. В то же время добиться увеличения прочности, как у горячепрессоваппых материалов [6], не удалось. Это связано с окислением пористых образцов не только на поверхности, но и по всему сечению, вследствие чего жидкая оксидная фаза может образовываться во внутренних слоях. Следовательно, отрицательное влияние окисления на пористые материалы сказывается сильнее, в то время как положительное влияние очистки от примесей — слабее из-за меньшего времени выдержки. Скорость диффузии примесей к поверхности также снижается: градиент концентрации кислорода по сечению образца уменьшается вследствие образования оксидной фазы на поверхности пор, пронизывающих весь образец. Увеличение времени выдержки, как было показано в [8], не изменяет сколько-нибудь существенно прочности материала.
Окисление при 1400°С, как отмечалось ранее |8], приводит к некоторому понижению прочности при комнатной температуре (таблица). Это связано с отрицательным влиянием сильных внутренних напряжений, возникающих в поверхностном слое окисленных образцов, а также с образованием пор, трещин и других дефектов в застывшем оксидном слое. В то же время предел прочности образцов, с поверхности которых был удален оксидный слой, возрос на 20 % по сравнению с исходным материалом. Такое увеличение предела прочности может быть вызвано залечиванием дефектов во внутренних слоях материала. Так как рентгенофазовым анализом обнаружить оксидные фазы в этих образцах не удалось, можно предположить, что окисление приводит к образованию тонкого слоя аморфного диоксида кремния на поверхности открытых пор.
Выводы.
Окисление реакционно спеченного материала на основе нитрида кремния при температуре 1400°С с последующим удалением оксидного слоя позволяет увеличить его прочность при 20 °С на 20 %. В то же время кратковременная прочность при 1400°С после такой обработки снижается по сравнению с неокисленными образцами, хотя и превосходит прочность окисленных, с поверхности которых не был удален оксидный слой.
Увеличение прочности образцов после окисления связано в основном с тем, что дефекты в подповерхностных слоях керамики залечиваются оксидной фазой, а также с очисткой внутренних слоев от примесей. Снижение прочности обычно вызывается формированием на поверхности образцов оксидного слоя с высокой концентрацией дефектов или возникновением значительных внутренних напряжений.
2. Подобеда Л. Г. Влияние примесей на свойства материалов из нитрида кремния // Порошковая металлургия.— 1979.— № 1.—С. 75—80.
3. Mangels J. Л. The effect of silicon purity on the strength of reaction-bonded Si3N<// J. Mater. Sci.— 1980.— 15, N 8.— P. 2132—2135.
4. Andersson С. A. Ceramic Materials for High-Temperature Turbines//Proc. workshop on cer. for adv. heat engines.—Orlando, 1977.—P. 183—189.
5. Высокотемпературное окисление конструкционной керамики на основе нитрида кремния / В. А. Лавренко, Э. А. Пугач, А. Б. Гончарук и др. // Порошковая металлургия.— 1984.—№ П.—С. 50—54.
6. Lange F. F., Davis В. Т., MetcalJ A. I. Strengthening of polyphase SisN* material through oxidation//J. Mater. Sci — 1983— 18, N 5 —P. 1497-1505.
7. Гогоци Г. А. Некоторые результаты изучения механических свойств конструкционной керамики применительно к деталям двигателей.— Киев, 1983.— 66 с.— (Препринт/Ин-т пробл. прочности АН УССР).
8. Гогоци 10. Г., Сопенко С. И., Трунов Г. В. Влияние окисления на прочность нитрид-кремниевой керамики//Пробл. прочности.— 1985.—№ 1.— С. 69—72.
9. Трощенко В. Т. Применение статистических теории прочности к расчету детален из жаропрочных керамических материалов//Вопр. прочности металлокерам. жаро-нроч. материалов.—1957.—Вып. 4.— С. 16—28.
10. Воздействие солей на прочность и трещнностонкость ннтрндкремнисвой керамики/ Г. А. Гогоци, 10. Г. Гогоци, В. П. Завада, С. И. Сопенко // Пробл. прочности.— 1984.—№ П.—С. 17—21.
11. Ziegler С. Thermal cycling behaviour of reaction-bonded silicon nitride and some microstructural effects"//Proc. Brit. Cer. Soc—1982,—N 32.—P. 213—225.
12. Evans A. C, Davidge R. W. The strength and oxidation of reaction sintered silicon nitride//J. Mater. Sci.— 1970.- 5, N 4.— P. 314—325.
13. Лавренко В. А., Гогоци Ю. Г.. Францевич И. //. Высокотемпературное окисление го-рячепрессовашюго карбида бора//Докл. АН СССР.—1984.—275, № 1.—С. 114— 117.
BibTex
@article {author = {Gogotsi, Alexey and Gogotsi, Yury and Scherbina O},
title = {Effect of oxidation on the strength of silicon nitride base reaction sintered ceramics},
journal = {Poroshkovaya Metallurgiya},
volume = {5},
number = {281},
url = {http://dx.doi.org/10.1111/j.1744-7402.2012.02843.x},
pages = {40-44},
year = {1986},
}
BibTex